Experimenteren om te optimaliseren met Design of Experiments (DOE)
Dagelijks gebruiken organisaties het woord "experimenteren" in de betekenis van "we proberen iets". Slechts zelden gebruiken we hierbij statistiek. Nochtans kan het ons veel werk besparen, zeer interessante inzichten verschaffen en heel veel financieel voordeel opleveren.
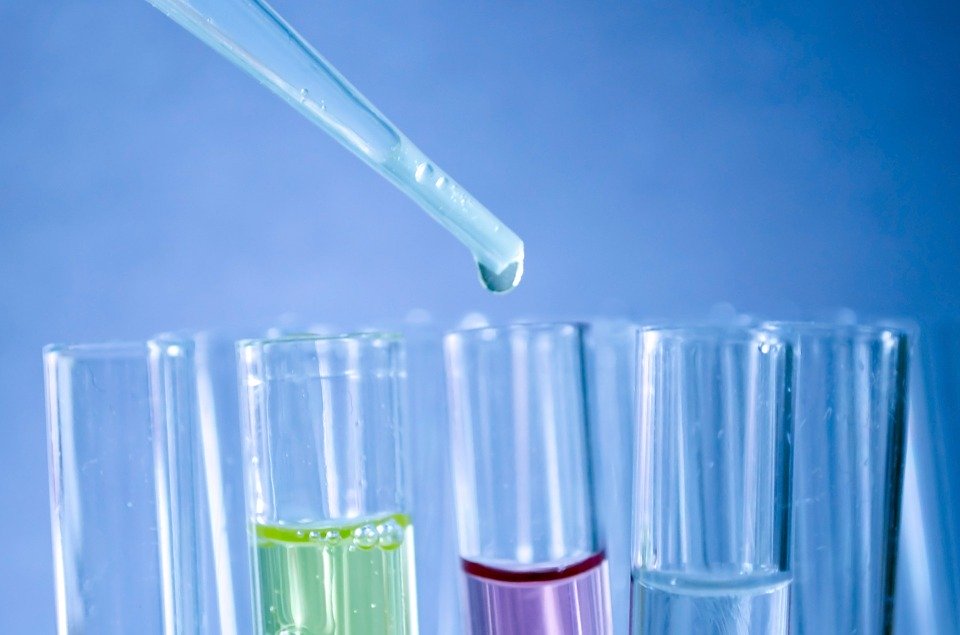
Een proces optimaliseren via 'trial & error'?
Een producent van coatingmachines heeft een nieuwe machine ontwikkeld. Om deze machne op punt te stellen voor een nieuwe toepassing, voert hij een aantal testen uit met 4 instelbare machineparameters: coatingduur (min), stroom (A), gasdebiet (cc/min) en spanning (V). Bij elke testcombinatie worden 2 stukken gemaakt.
Het doel van deze reeks testen is de ideale combinatie te vinden van parameters die leidt tot enerzijds een uniforme laagdikte (targetwaarde = 1,45 μm) en anderzijds een Vickers hardheid van 1500 HV bij 20mN. Hieronder staat een schematische voorstelling.
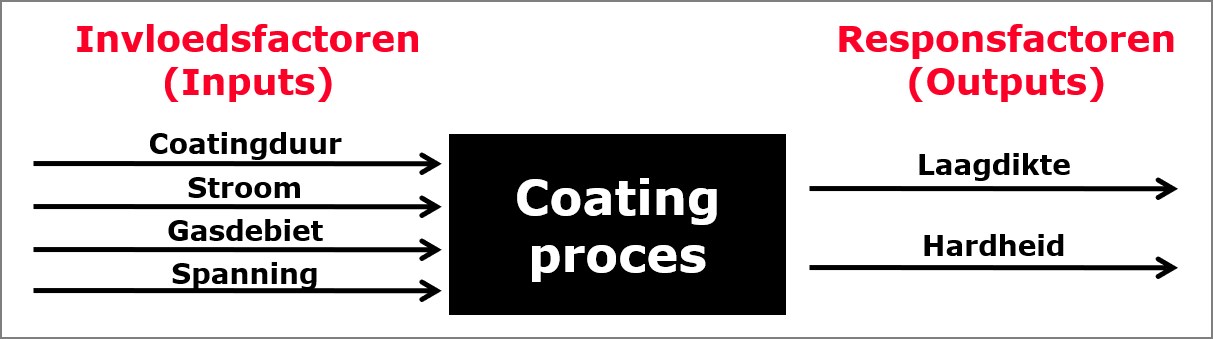
Op basis van de reeds aanwezige proceskennis worden via 'trial & error' in totaal maar liefst 38 testen uitgevoerd. De resultaten worden voorgesteld in onderstaande tabel.
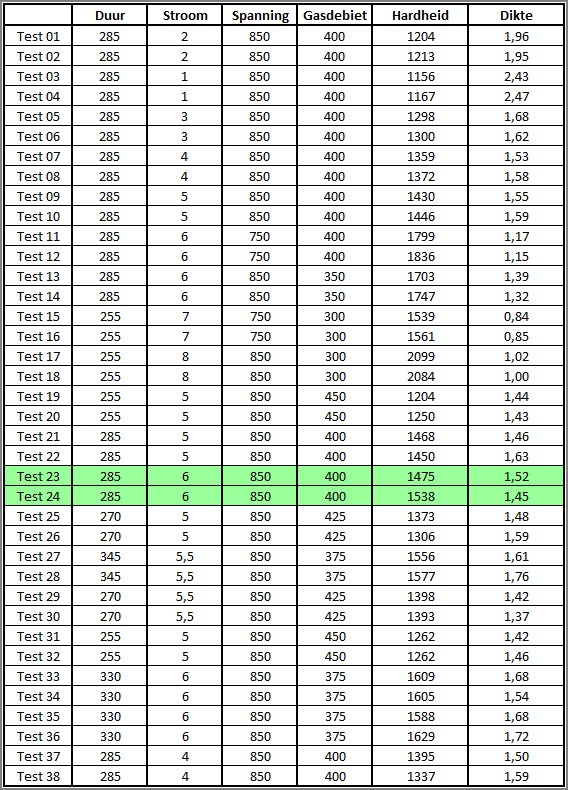
Uiteindelijk wordt een combinatie van factoren geselecteerd (aangeduid in het groen) als zijnde de ideale combinatie die resulteert in de gewenste laagdikte van 1,45 μm met een hardheid van 1500 HV.
Veel experimenteren, weinig leren...
De Engineering Manager, verantwoordelijk voor het optimaliseren van de coatingmachine, is slechts matig tevreden over het resultaat van de uitgevoerde experimenten. Het doel is weliswaar bereikt, maar de bovenstaande experimenten hebben ontzettend veel tijd in beslag genomen (in totaal 1 maand testen), veel geld gekost (38 teststukken gemaakt) en hebben in feite bitter weinig bijkomend inzicht in het coatingproces opgeleverd. Immers, het enige wat de onderzoekers geleerd hebben, is welke combinatie leidt tot een goed resultaat. Deze combinatie is echter niet noodzakelijk de enige, de goedkoopste, de meest efficiënte, ...
Tevens werd er niets geleerd over het belang van elk van de regelbare parameters: welke parameters spelen een belangrijke rol, welke hebben een onbeduidende invloed, ...
Design of Experiments als alternatieve aanpak
Na het volgen van een opleiding over opleiding over opleiding over "Design of Experiments (DOE)" beslist de Engineering Manager om het optimalisatieproces helemaal opnieuw uit te voeren, los van de reeds uitgevoerde experimenten. Zijn doel is te bewijzen dat het efficiënter kan (met minder uit te voeren experimenten) door enerzijds de experimenten planmatiger en systematischer aan te pakken, en anderzijds ook statistiek te gebruiken. Om zijn slaagkansen te maximaliseren doet de man beroep op Jan Libbrecht, de docent die de opleiding DOE verzorgd heeft, om zich te laten begeleiden.
Na bespreking met de consultant wordt het voor de Engineering Manager duidelijk dat er in feite slechts drie stuurbare parameters zijn (stroom, gasdebiet en spanning), en dat de vierde parameter (coatingduur) in feite een output parameter is, gelinkt aan de laagdikte. Immers, hoe langer er gecoat wordt, hoe dikker de laagdikte. Daarom wordt er gekozen om een nieuwe output parameter te meten, namelijk de depositiesnelheid.
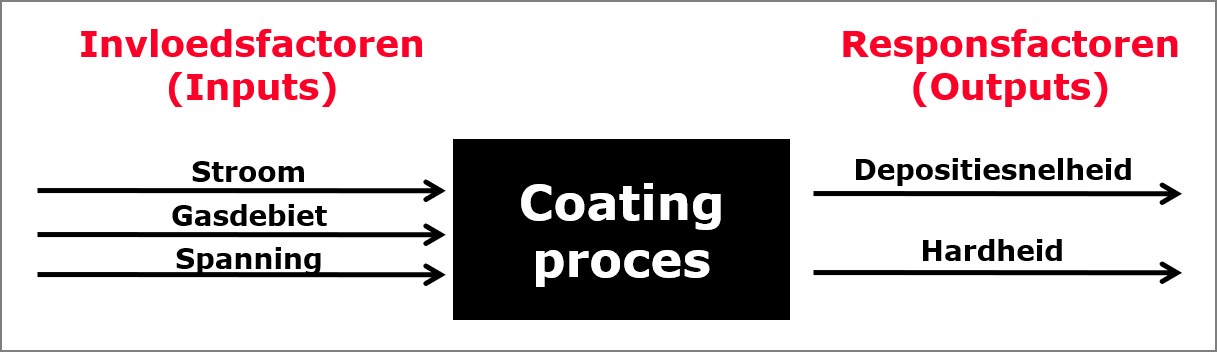
Een wiskundig model kiezen
In DOE zijn er enorm veel verschillende proefschema's mogelijk, elk met hun voor- en nadelen. Aangezien we niet-lineariteit verwachten, houden we het aantal experimenten zo laag mogelijk en opteren we voor een Box-Behnken experiment met 3 factoren:
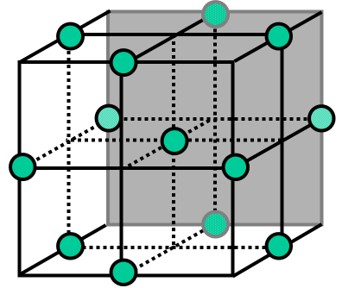
Een dergelijk proefopzet voor 3 factoren bevat 15 unieke experimentele combinaties. De tabel 5 geeft deze combinaties weer, samen met de meetresultaten voor hardheid en depositiesnelheid.
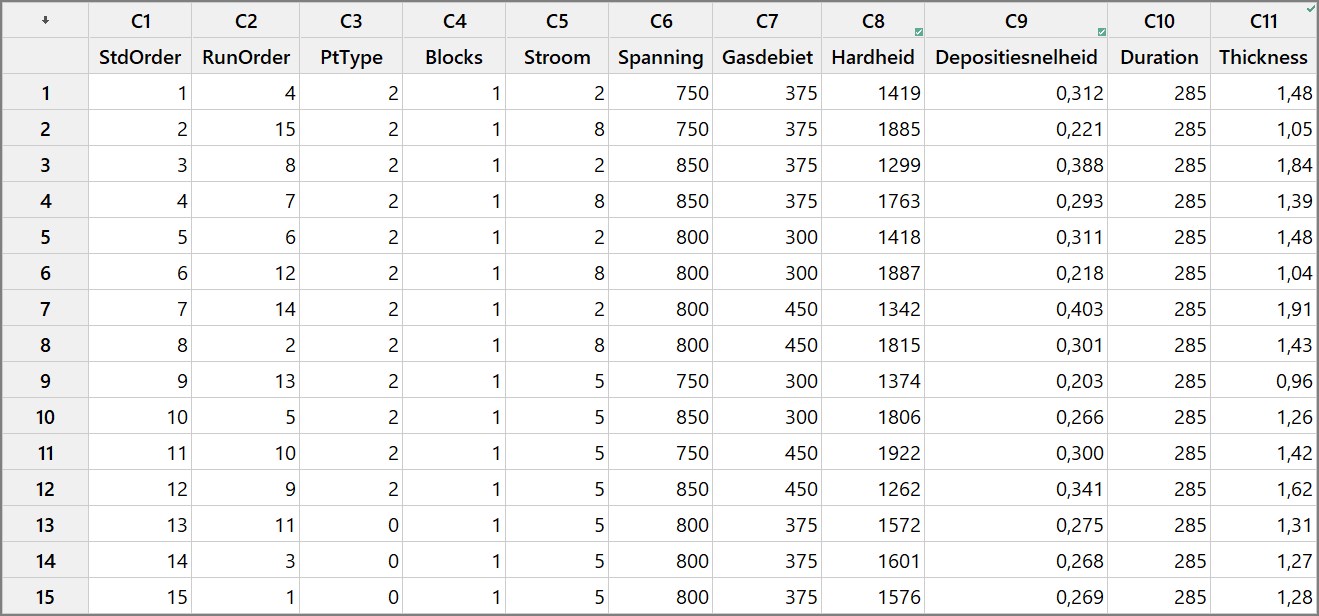
Met behulp van het statistisch pakket Minitab bepalen we nu zowel voor de hardheid als voor de depositiesnelheid een wiskundig model op basis van de gemeten resultaten. Het resulterend wiskundig model bevestigt de resultaten van de oorspronkelijke analyse met 38 testen: een hardheid van 1500 en een dikte van 1,45 (depositiesnelheid 0,308 bij 285 minuten) kan gerealiseerd worden bij een stroom van 6 A, een spanning van 850 V en een gasdebiet van 400 cc/min:
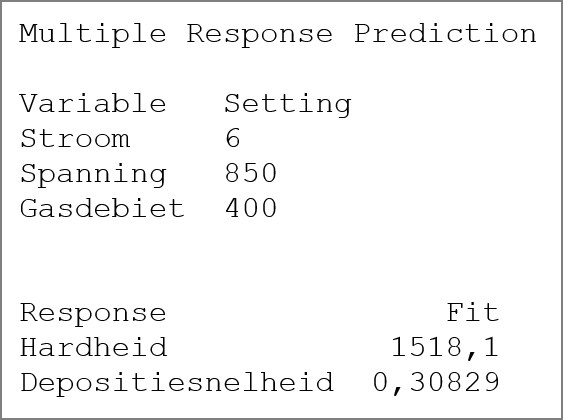
Bijkomend kunnen we nu ook de invloed van elke parameter op het proces beoordelen.
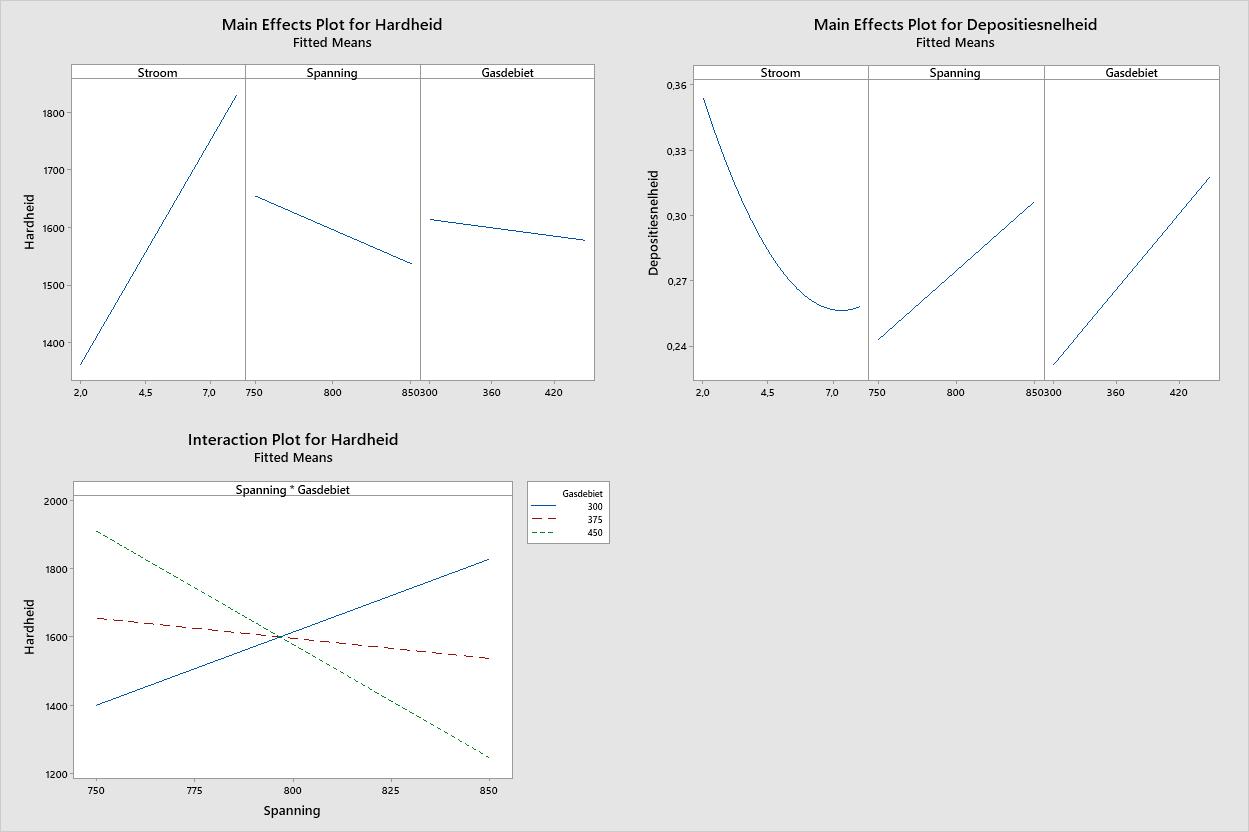
De kassa begint te rinkelen...
Op basis van de verworven inzichten kunnen we het proces nog verder optimaliseren: door de stroom en de spanning te verlagen en terzelfdertijd het gasdebiet te verhogen, kan eenzelfde hardheid en dikte gerealiseerd worden met een veel hogere depositiesnelheid van 0,38 i.p.v. 0,31. Met andere woorden: in plaats van 285 minuten coatingtijd zijn nu slechts 230 minuten per stuk nodig: een winst van drie kwartier per stuk of 19% sneller!
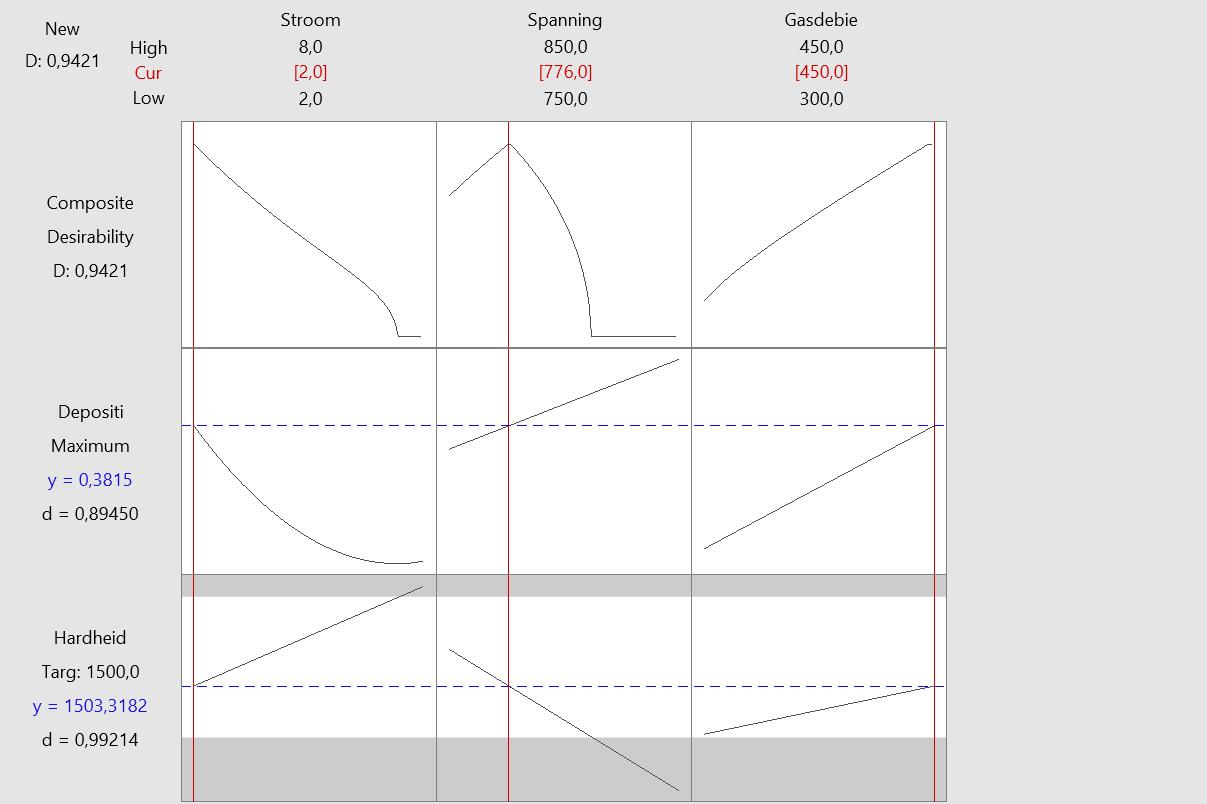
Bovendien kunnen we het mathematisch model ook verder gebruiken om de sensitiviteit van de gekozen instellingen te evalueren: zolang de parameters binnen de witte zone blijven is een goed resultaat gegarandeerd :
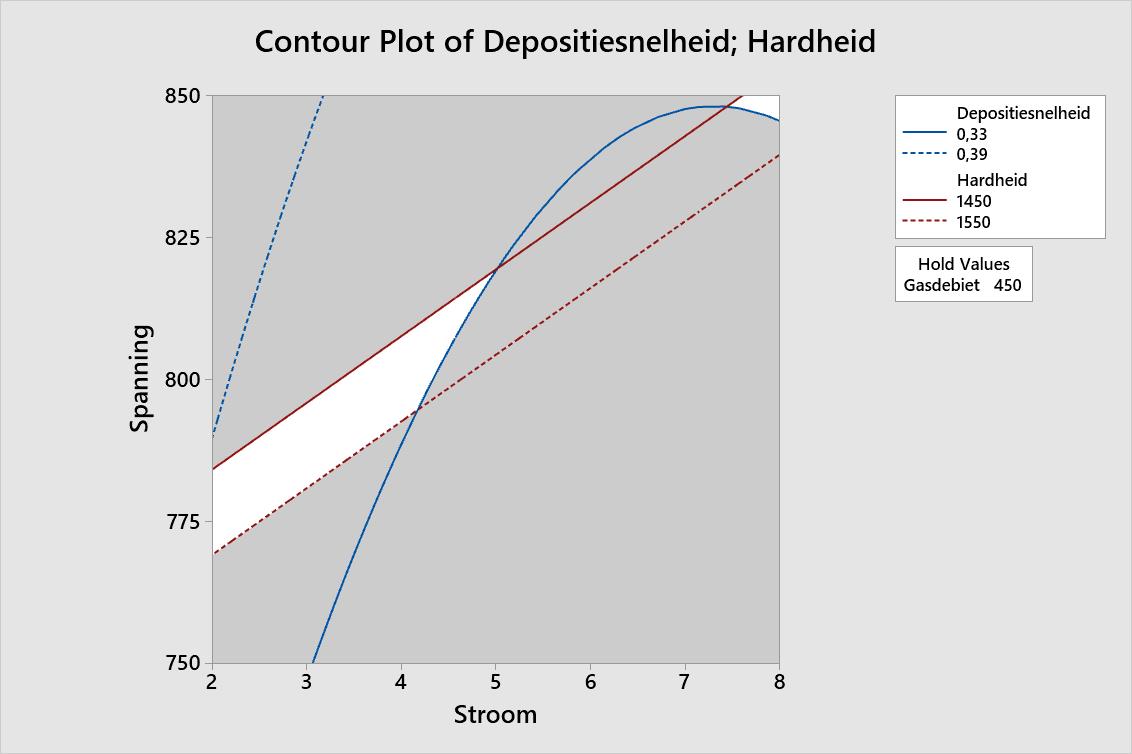
De Engineering Manager is overtuigd en zeer tevreden: het proces is inzichtelijk geworden, er waren slechts 15 experimenten nodig in plaats van 38 en het resultaat is een geoptimaliseerd proces dat sneller en goedkoper is.